Electrically Conductive Adhesives Expand
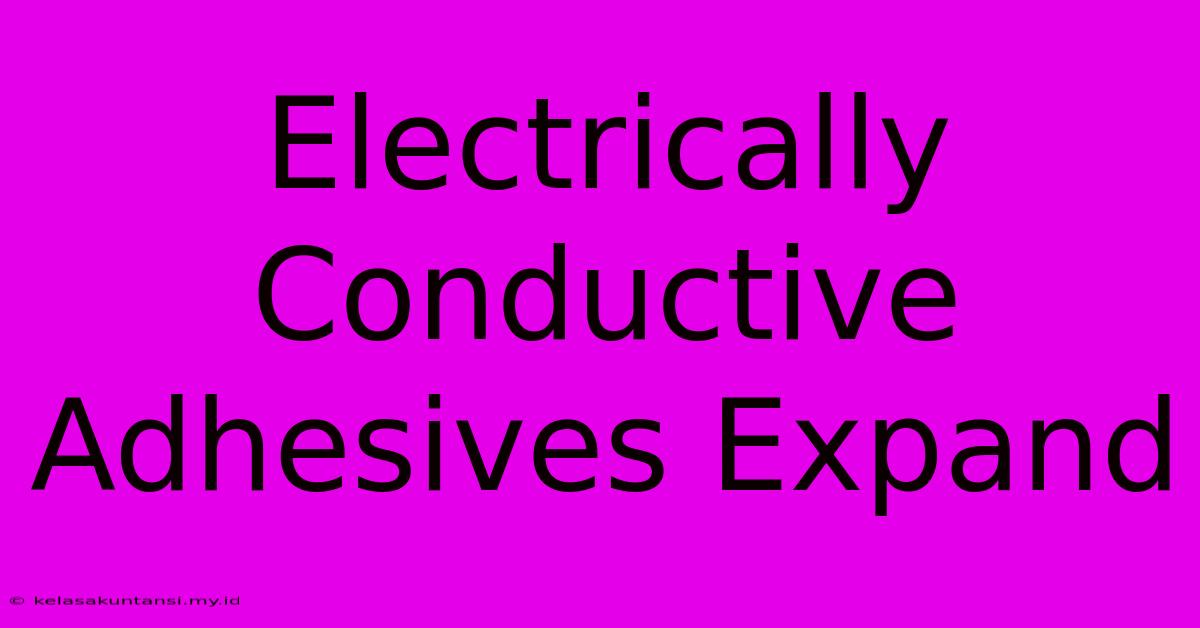
Temukan informasi yang lebih rinci dan menarik di situs web kami. Klik tautan di bawah ini untuk memulai informasi lanjutan: Visit Best Website meltwatermedia.ca. Jangan lewatkan!
Table of Contents
Electrically Conductive Adhesives Expand: A Comprehensive Guide
Electrically conductive adhesives (ECAs) are experiencing a significant expansion in their application across diverse industries. Their unique properties, combining electrical conductivity with adhesive strength, are driving this growth. This comprehensive guide explores the expanding world of ECAs, detailing their functionalities, applications, and future prospects.
What are Electrically Conductive Adhesives?
Electrically conductive adhesives are specialized materials that provide both strong adhesion and excellent electrical conductivity. Unlike traditional solder, ECAs offer several advantages, including:
- Lower processing temperatures: This is crucial for temperature-sensitive components.
- Flexibility: ECAs can accommodate movement and vibration, unlike rigid solder joints.
- Ease of application: They can be applied using various techniques like screen printing, dispensing, or jetting.
- Isotropic conductivity: Conductive pathways can be formed in any direction.
These features make ECAs ideal for a wide array of applications.
Types of Electrically Conductive Adhesives
Several factors influence the classification of ECAs, including their conductive filler, base polymer, and curing mechanism. Common conductive fillers include:
- Silver: Offers high conductivity but can be expensive.
- Copper: A cost-effective alternative with good conductivity.
- Nickel: Provides excellent corrosion resistance.
- Carbon: A low-cost option, but with lower conductivity.
The choice of filler depends heavily on the specific application requirements and budget considerations.
Expanding Applications of Electrically Conductive Adhesives
The versatility of ECAs fuels their expanding use in various sectors:
Electronics Manufacturing
ECAs are crucial in modern electronics assembly. Their use in:
- Chip packaging: Connecting chips to substrates.
- Flexible circuits: Creating reliable connections in bendable electronics.
- LED lighting: Assembling LED components.
- Automotive electronics: Connecting sensors and actuators.
demonstrates their importance in miniaturization and innovation.
Medical Devices
The biocompatibility of certain ECAs makes them suitable for:
- Implantable devices: Creating secure and conductive connections within the body.
- Sensors and actuators: Integrating electronic components into medical instruments.
The reliability and safety of ECAs are vital in this sensitive sector.
Other Industries
Beyond electronics and medicine, ECAs are finding their way into diverse applications, including:
- Aerospace: Connecting sensitive components in harsh environments.
- Solar energy: Creating conductive pathways in solar cells.
- Wearable technology: Connecting components in flexible wearable devices.
The ongoing research and development in ECA technology will continue to broaden their applications.
The Future of Electrically Conductive Adhesives
Research focuses on developing ECAs with:
- Improved conductivity: Higher performance for demanding applications.
- Enhanced reliability: Longer lifespan and increased stability.
- Better processability: Easier and more efficient application methods.
- Environmentally friendly materials: Reducing the environmental impact of manufacturing.
This continuous innovation ensures that electrically conductive adhesives will continue to expand their presence in various technological advancements.
Frequently Asked Questions (FAQs)
Q: Are electrically conductive adhesives suitable for high-temperature applications?
A: While some ECAs can withstand moderate temperatures, their upper temperature limit is generally lower than that of traditional solder. Specific temperature resistance depends heavily on the chosen ECA formulation.
Q: How is the conductivity of an ECA measured?
A: Conductivity is typically measured in Siemens per meter (S/m) or ohm-cm. The specific testing method depends on the adhesive's form and application.
Q: What are the limitations of ECAs?
A: While ECAs offer many advantages, their limitations include lower conductivity compared to solder in some instances, potential sensitivity to moisture, and limitations in handling high currents in some formulations.
Conclusion:
Electrically conductive adhesives represent a remarkable advancement in materials science, offering versatile solutions for various applications. Their expanding use across diverse industries underscores their importance in modern technology and points to an exciting future of innovation in the field of ECA development. The continued refinement and exploration of ECAs promise even wider applications and increased performance in the years to come.
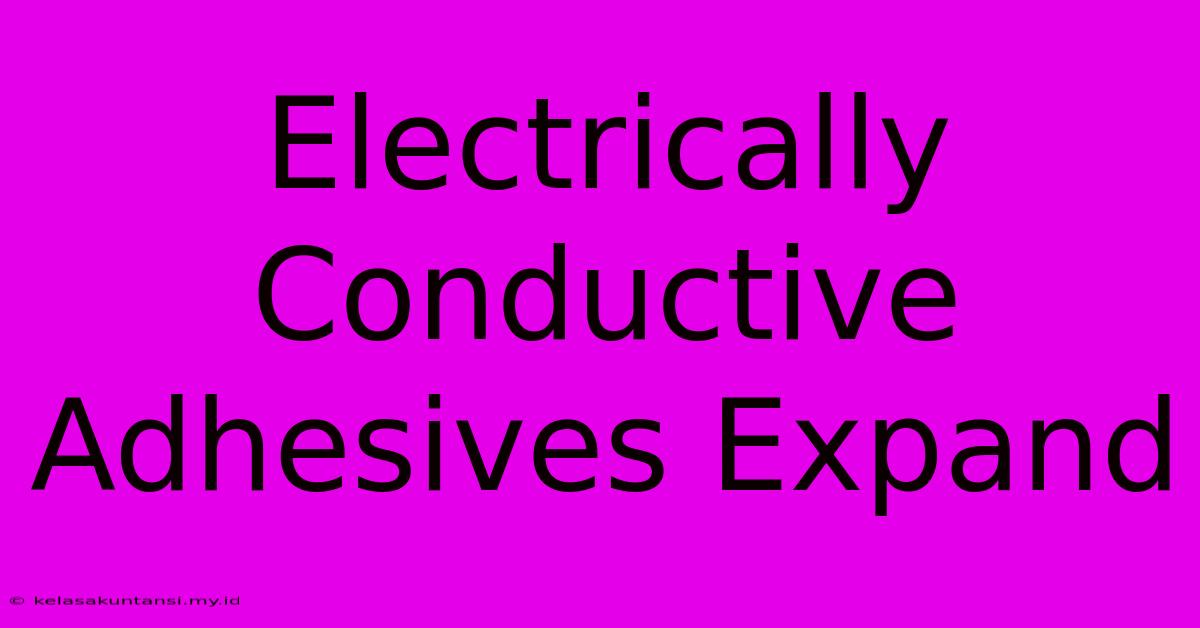
Football Match Schedule
Upcoming Matches
Latest Posts
Terimakasih telah mengunjungi situs web kami Electrically Conductive Adhesives Expand. Kami berharap informasi yang kami sampaikan dapat membantu Anda. Jangan sungkan untuk menghubungi kami jika ada pertanyaan atau butuh bantuan tambahan. Sampai bertemu di lain waktu, dan jangan lupa untuk menyimpan halaman ini!
Kami berterima kasih atas kunjungan Anda untuk melihat lebih jauh. Electrically Conductive Adhesives Expand. Informasikan kepada kami jika Anda memerlukan bantuan tambahan. Tandai situs ini dan pastikan untuk kembali lagi segera!
Featured Posts
-
Mlb Draft Lottery Nationals Win
Dec 11, 2024
-
Champions League Benfica Setzt Auf Heimvorteil
Dec 11, 2024
-
Winter Meetings Sasaki Crochet Updates
Dec 11, 2024
-
Domingo Reportaje Sobre El Trafico De Ketamina
Dec 11, 2024
-
El Psg Resucita Tras Dificil Momento
Dec 11, 2024